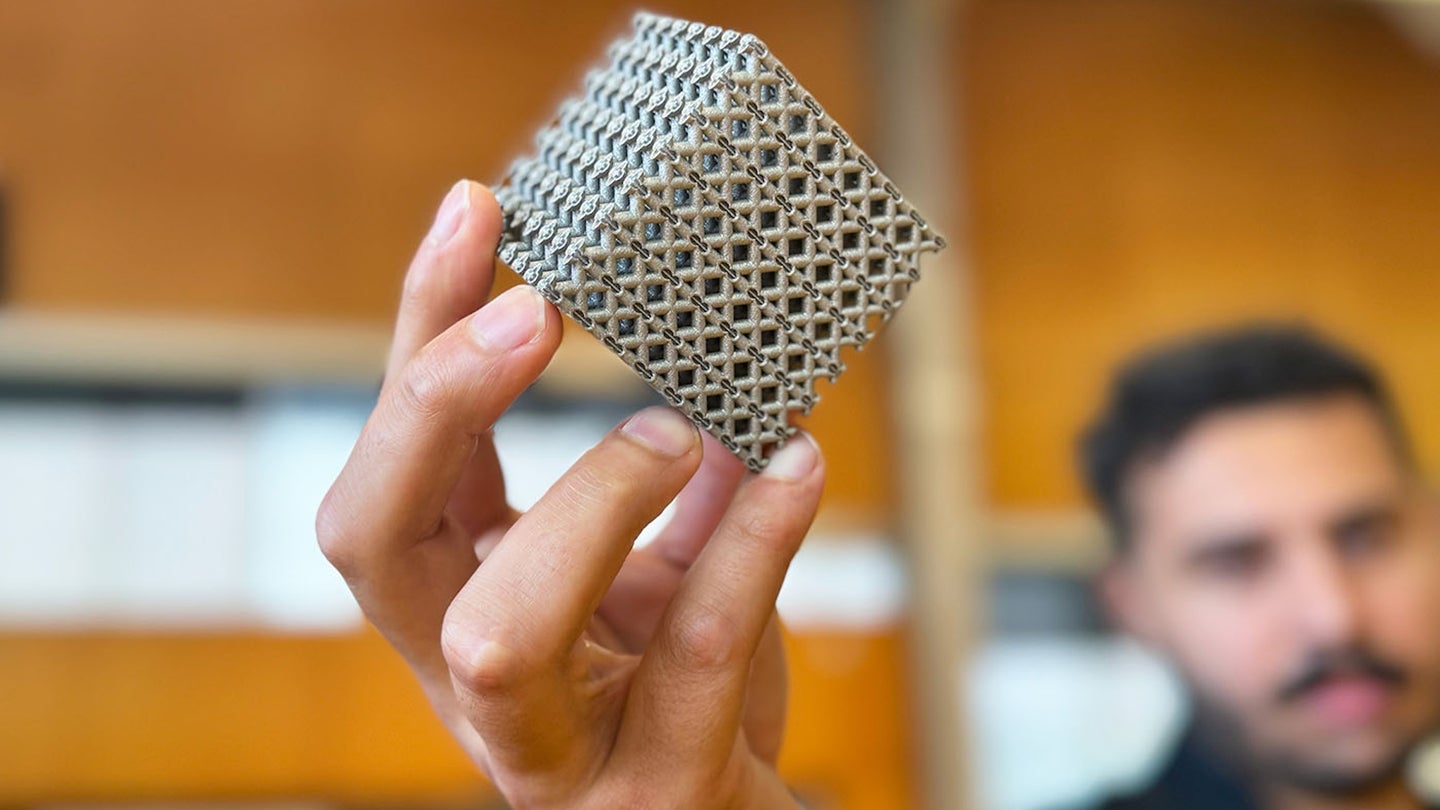
Cellular structures made from metal alloys could strengthen everything from bone implants to rocket parts—if they didn’t keep cracking under pressure. Researchers have so far spent years attempting to solve for uneven weight distribution issues across these artificial “metamaterials” to little success. As detailed in a recent study published in Advanced Materials, however, a team at Australia’s RMIT University appears to have finally figured out the solution after drawing inspiration from plants and coral, with some help from a cutting-edge 3D-printing tool.
Using a common titanium alloy, engineers manufactured latticelike structures composed of hollow struts—each imbued with an additional, thin band running throughout it. According to Ma Qian, an RMIT Distinguished Professor of advanced manufacturing and study co-author, the team combined “two complementary lattice structures to evenly distribute stress, we avoid the weak points where stress normally concentrates.”
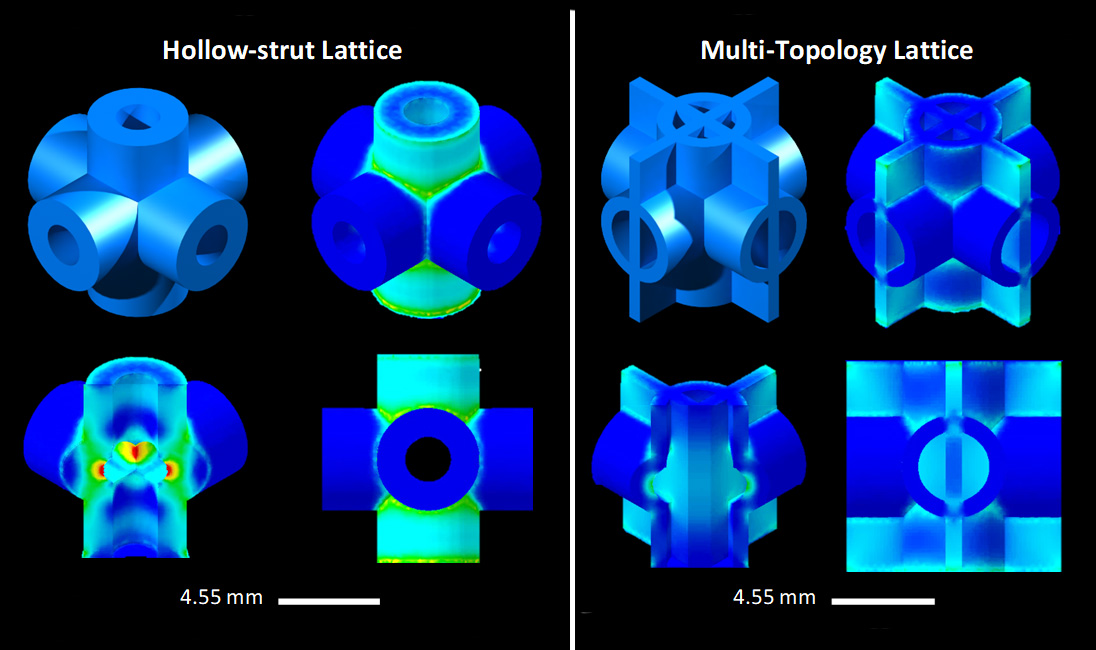
“These two elements together show strength and lightness never before seen together in nature,” Qian continued in a university profile published on Monday.
To construct their lattice metamaterials, researchers utilized a highly advanced manufacturing process known as laser powder bed fusion, in which a powerful laser beam flash-melts layered titanium granules directly into place. Subsequent stress tests of a cube made from the new, hollow latticework withstood 50-percent more weight than a similarly dense cast of WE54, a magnesium alloy commonly used for aerospace engineering.
Although the resilient metamaterial can already withstand temperatures up to 350-degrees Celsius (662 Fahrenheit), its makers believe that utilizing more heat-resistant titanium alloys could raise that threshold up to 600-degrees Celsius (1,112 Fahrenheit). If so, the metalwork could find more uses in rocketry manufacturing, and even firefighting drones.
[Related: Titanium-fused bone tissue connects this bionic hand to a patient’s nerves.]
Meanwhile, the team thinks these lattice structures could also prove useful in human bone implants, since their hollowness may allow for bone cell regrowth as the equipment fuses with a patient’s body.
That said, it might be a little while before the titanium metamaterial becomes commonplace. As study lead author and PhD candidate Jordan Noronha explained in RMIT’s feature, “Not everyone has a laser powder bed fusion machine in their warehouse.”
Still, Noronha, Qian, and their colleagues believe technological advances and increased equipment accessibility will eventually make it easier for others to also harness their metamaterial design.
The post A 3D-printed titanium ‘metamaterial’ design solved a longtime engineering issue appeared first on Popular Science.
Articles may contain affiliate links which enable us to share in the revenue of any purchases made.
from Popular Science https://ift.tt/WjgqG98
0 Comments