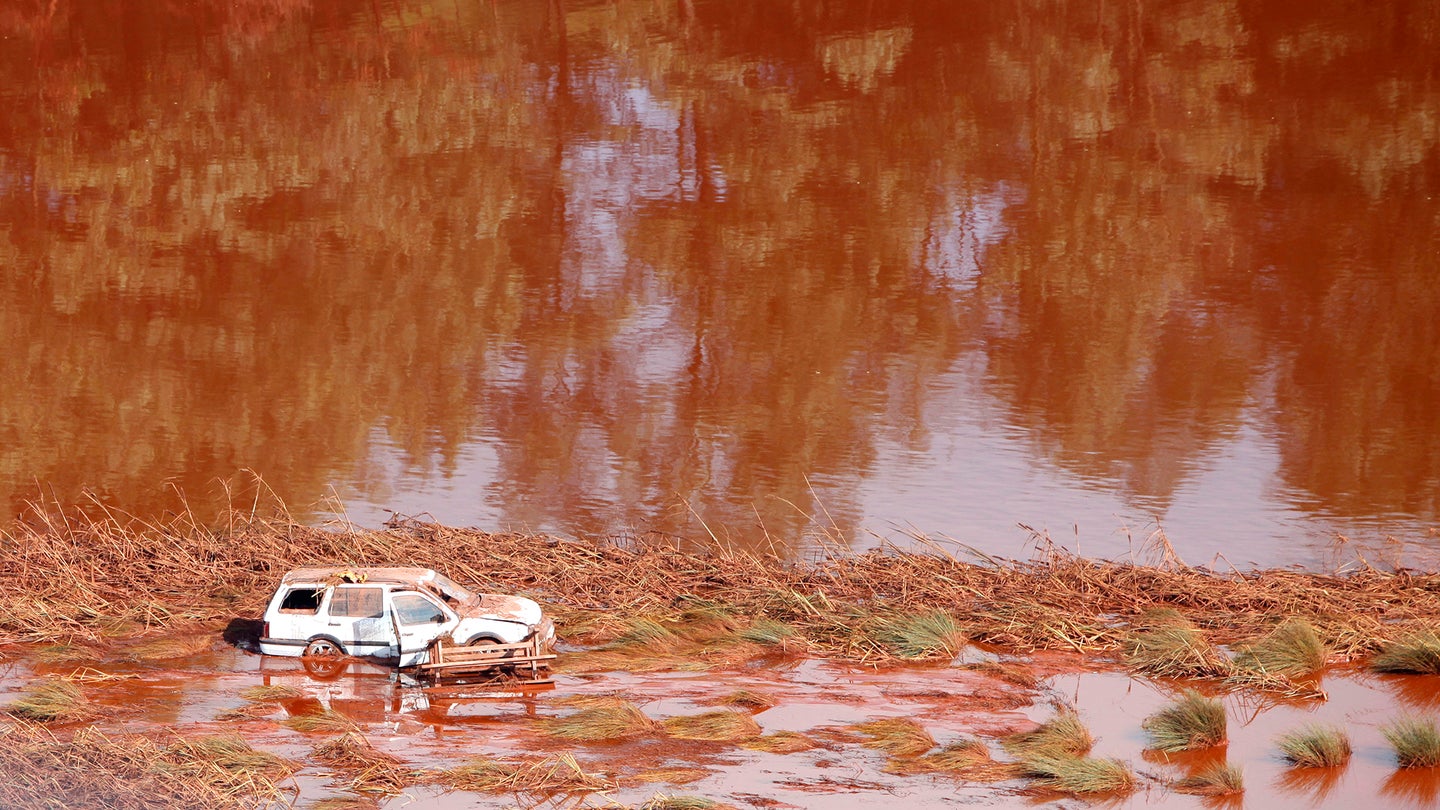
Making aluminum is dirty work, and hasn’t improved much since the 1886 debut of its most widespread production method. Aside from all the carbon emissions, the ubiquitous metal’s smelting process also creates massive amounts of a toxic red mud byproduct with a pH level often rivaling commercial bleach or engine cleaner. The caustic gunk is usually relegated to giant landfills, unless something like an industrial accident unleashes torrents of the sludge, as was unfortunately the case for rural Hungarian residents back in 2010.
But if there’s anything worse than aluminum manufacturing, it’s steel, which accounts for about 8 percent of all CO2 emissions. In order to reduce the industry’s damaging impact, many researchers and companies are working towards a “green steel” future—strategies such as swapping out the dirty power sources in steel factories for renewable energy, and integrating hydrogen or electric energy into production.
As many engineers continue focusing on reducing industrial smelting’s notorious emission issues, a team at the Max-Planck-Institut für Eisenforschung has developed a way to quickly and affordably recycle aluminum’s red mud byproduct for use in green steel projects with a little help from hydrogen plasma.
[Related: Inside the high-powered process that could recycle rare earth metals.]
The researchers’ paper, recently published in Nature, details how the aluminum industry could one day account for its annual generation of an estimated 198 million tons of red mud—a number expected to only grow larger as demand for the material increases.
For the scientists, it’s a (relatively) simple procedure. Red mud is deposited in an electric arc furnace, where it is subjected to the extremely high temperatures of a plasma containing 10 percent hydrogen. The intense heat then melts down the mud, which separates into liquid metal oxides. As much as 60 percent of red mud is iron oxide, which subsequently transforms into a liquid iron so pure that it can immediately be used in steel production. All told, the “plasma reduction” process takes just 10 minutes to complete.
Meanwhile, the furnace heat largely neutralizes any other leftover oxides’ corrosiveness, including heavy metals like chromium. Scientists believe with further investigations, these valuable metals could also be separated for reuse, thus lessening the chance for them to otherwise leach out of red mud into the environment. After all that, everything remaining in the furnace then cools into glass-like residuals that researchers think could be useful as various filling materials in the construction industry.
While the test utilized only 15g of red mud (yielding 2.6g of metallic iron), the team calculated that their process is both economically viable and industrially scalable. In a recent university profile, research group leader Isnaldi Souza Filho estimates that around 770 million tons of CO2-free steel could derive from the world’s existing 4.7 billion tons of red mud—about one-third of annual steel production’s needs.
“Our process could simultaneously solve the waste problem of aluminum production and improve the steel industry’s carbon footprint,” added Matic Jovičevič-Klug, another scientist involved in the study.
Because electric arc furnaces are already widespread within metal production, it would only take a proportionally small investment to ready them for this new process. With some additional research and adjustments, aluminum’s longtime, notoriously noxious waste could finally become something useful—and far more eco-friendly.
The post Aluminum’s notorious, toxic red mud could one day help make ‘green steel’ appeared first on Popular Science.
Articles may contain affiliate links which enable us to share in the revenue of any purchases made.
from Popular Science https://ift.tt/ecT28jB
0 Comments